We offer custom made solutions for
Steel Making
We offer process measurement and optimization solutions in both the primary and secondary steelmaking process steps. Improving yield, safety and process control at the steel making stage has a huge positive impact down streams. Discover our solutions specifically aimed towards the BOF, EAF, Ladles, LF and RH areas.
Iron Making
Operation safety and innovative process consistency solutions are making sure our customers can achieve the set targets and reach the throughput demands. Our solutions for iron making enhances the safety of operation and increases the process control.
Continuous Casting
Few companies in the world can offer measurement packages covering the complete continuous casting process, from the ladle to the mold. Discover our continuous casting solutions for slag detection, level measurement and ladle integrity that together or as standalone systems ensures process excellence and safety of operation.
Non-Ferrous Solutions
We provide unique material level profile information in smelting furnaces such as metal and slag level measurement. Our patented technology gives you the power to understand and control your process. Our equipment enhances safety for your personnel while providing consistently accurate measurements and are typically used in Flash-, TSL-, SAF-, SC- and Rotary furnaces to measure bath levels on demand or continuously.
Here are examples of some of two of our solutions
Solutions that maximize efficiency and margins:
Example: Full Line Service
A Single basic oxygen furnace (BOF) demands different types of refractories designed according to their distinct physical and thermo-chemical properties.
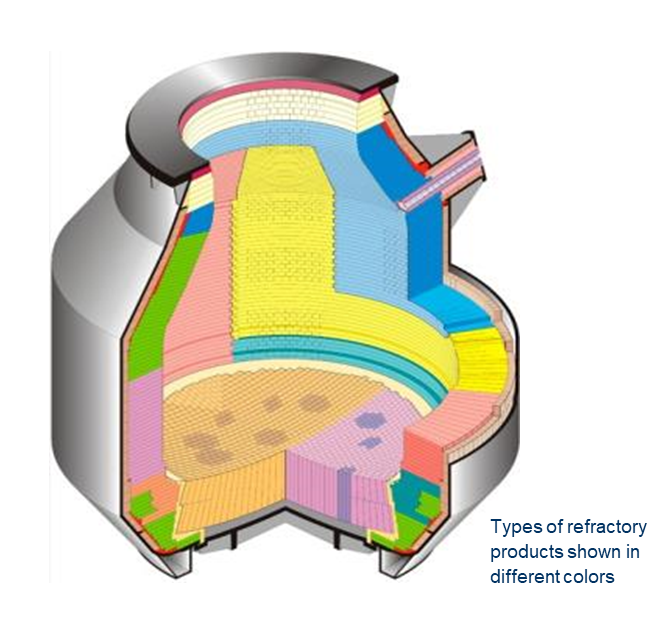
One key objective for Full Line Service clients is to develop refractories that last longer and are consumed homogeneously within each equipment for each customer in each plant.
Refractory consumption on the converter walls was diagnosed as heterogeneous, potentially leading to premature disposal of other refractories within the converter. Replacing an entire wall would lead to higher downtime of the equipment and more refractory use.
The solution consisted of:
-
Identifying the compromised area in the BOF converter
-
Applying lower-cost gunning mixes in order to increase the lifetime of still-good refractories
-
Higher refractory efficiency led to higher margins for both RHI Magnesita and the customer
-
Finally, refractories were sent for post-mortem analysis and allowed for adjustments to customer process and refractory composition to increase homogeneity.
Tailor-made products and services that drive performance and cost savings.
Example: Implementing Gas Purging in Electric Arc Furnaces for High-Alloyed Steelmaking Stainless steel production has significantly different EAF process conditions compared to low-alloyed steelmaking due to the oxidation characteristics of Chromium during decarburization of the molten metal.
Benefits of gas purging:
-
Decreased melting time of scrap and DRI
-
Increased heat transfer during the superheating period
-
Decreased specific electrical energy demand
-
Enhancing mixing of the steel melt and increasing homogeneity
-
Avoidance of unwanted skull formation or debris
-
Decreased deviation between the measured steel temperature in the EAF and the ladle furnace
Immediate process improvement and client cost savings
120t EAF |
Before |
After |
 |
Charged weight (t) |
126.3 |
126.7 |
+0.4 |
Tap Weight (t) |
122.9 |
127.9 |
+5.0 |
Yield (%) |
87.9 |
92.4 |
+4.5 |
FeSi (kg) |
290 |
222 |
-23% |
Lime/Dolomite (t) |
4.45 |
4.14 |
-7% |
Power-on time (min) |
102 |
108 |
+6 |
Tap Temperature (°C) |
1.571 |
1.572 |
+1 |
Energy (kWh/t) |
543 |
526 |
-17 |
As a result, the vast majority of customers in high-alloyed and stainless steelmaking now use EAF gas purging as standard technology.